- June 12, 2023
- Perspectives, Trending Topics
Industrial Outdoor Storage: More Than a Parking Lot for Big Rigs
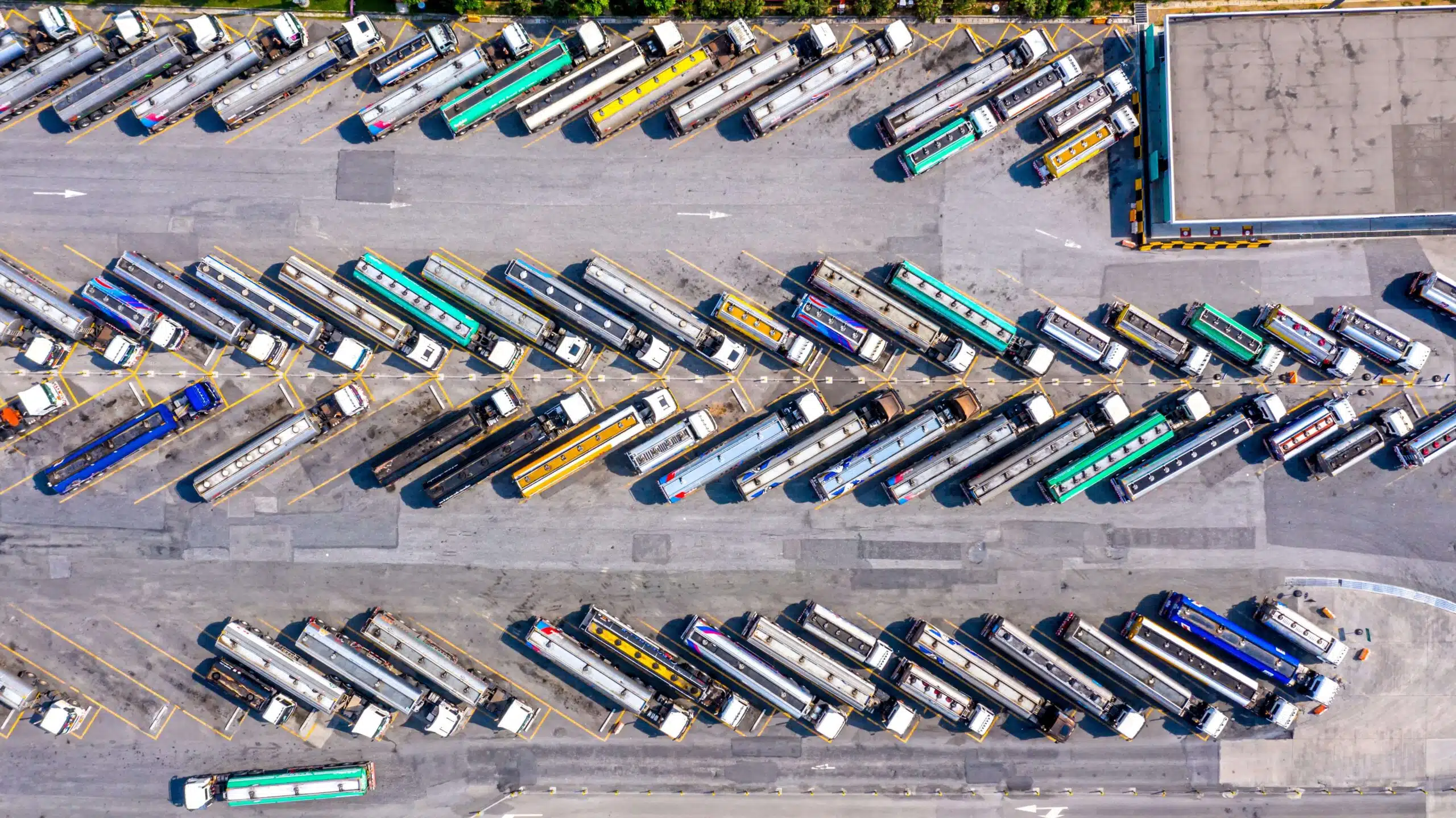
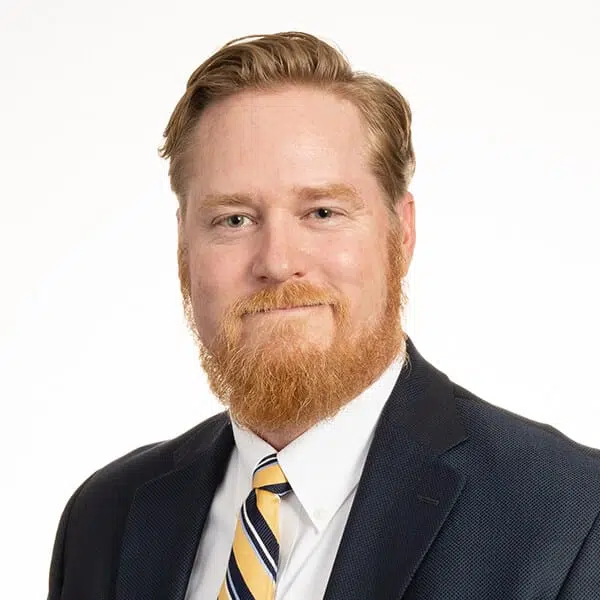
Dave France, PE
Industrial Practice Lead

Austin Watts, PE
Industrial Practice Lead
As more logistics, retail, and e-commerce businesses seek to expand and optimize their operations, increased consumer demand and shipping vessel capacity has led to ports wanting to move more containers off-site site quickly. To encourage this, many ports increased the cost to store containers on-site, creating a demand for lower-cost storage solutions like industrial outdoor storage (IOS)—also known as drop lots—which also provide flexibility for fluctuating storage needs.
This, along with a shortage of industrial warehouse real estate near ports and urban areas, has made IOS a billion-dollar opportunity for developers and investors seeking high occupancy rates and attractive returns.
Although there is a common belief among investors and developers that IOS is simply a space to park vehicles, IOS is a sophisticated and complex solution that involves careful planning, design, and construction to create a secure, efficient, and functional outdoor storage space. For these facilities to provide outdoor storage for tractor-trailers, industrial equipment, materials, and goods, expertise in local codes, an understanding of design requirements and constraints, and forethought regarding site amenities is required.
We’ve identified common challenges encountered during the permitting process and developed the following considerations you should know to ensure your project is designed and approved without delays or cost overruns.
Avoiding the Pitfalls of Industrial Outdoor Storage
The primary source of challenges is municipalities’ unfamiliarity with this type of project. Many cities and counties don’t have regulations or ordinances for outdoor storage facilities, which requires creativity to navigate permitting obstacles. Some municipalities may hesitate to approve projects due to concerns about property values or the community impact, while others may look to assign costly off-site improvements as conditions of approval.
As a result, developers may need to invest more time and resources in educating local officials and community members about IOS facilities. To overcome these challenges and speed up the permitting process, several conditions should be considered.
1. Design an Industrial Facility that Meets End-User Needs
Developers must carefully consider the facility’s operational needs to ensure it best serves users. A critical consideration is the ability for drivers to dwell on-site, which can impact noise levels, security, the need for restrooms, and air quality.
While an unstaffed facility may be less complicated to permit and design, it could lead to increased crime, and therefore more government and community hesitance. Providing a staffed guardhouse and bright site lighting can lower these risks, but it requires running utilities to bathrooms and other amenities. It also brings the potential for queueing and stacking at entrances (and ultimately onto public roadways).
Providing shore power to plug in can mitigate this issue, but it requires further access to utilities and adequate power. It’s also essential to be familiar with local codes that regulate hours of operation and noise requirements. A thorough concept plan covers jurisdiction requirements spanning not only the site, but also traffic and noise studies to accelerate the permitting process.
2. Get Creative With Trip Generation
The lack of code for IOS facilities makes it challenging for developers to determine the appropriate trip generation rates. To overcome this, developers must collaborate with the Authorities Having Jurisdiction (AHJ) to obtain buy-in. This is crucial when building an IOS facility for a specific user or to support a facility, as the developer must consider the owner’s exit strategies and ensure the facility can support future needs while also being cost-effective to build.
3. Consider Varying Trailer Sizes
Another crucial factor is the desired mix of trailer drop dimensions. Twenty Foot Equivalent Unit (TEU) is a standard unit of measurement in the shipping industry. Most international shipping containers are now Forty Foot Equivalent Units (FEUs), or two TEUs. Depending on the needs of the logistics center, a mix of 20- and 40-foot positions may be required. If trailers will stay attached to the tractor while they dwell, that requires yet a larger space. The most common domestic/interstate trailers are 53 feet long. The difference between 40-foot and 53-foot spaces affects the size and layout of the drop lot.
4. Prepare for Climate Impacts
Understanding the local climate and its potential impacts on the IOS facility helps ensure the facility’s safety, efficiency, and durability over time. In areas with intense winter weather, the facility must have proper snow storage areas and drainage to prevent ice buildup and allow safe vehicle access. High-wind areas require fencing and other barriers to prevent damage from wind and debris. Most sites will require stormwater management in the form of dry/wet ponds, sand filters, or underground detention.
5. Balance Screening and Security Considerations
Screening an industrial outdoor storage lot provides a measure of security and privacy for tenants and a visual block for neighbors. It can also vary depending on the location and the type of materials being stored. Some common screening methods include fencing and landscaping. Each of these methods has its advantages and disadvantages, and developers must assess the risks associated with each type. The key is to strike a balance between security and aesthetics that meets the needs of the tenants and the surrounding community.
6. Plan for Adaptive Use and Future Opportunities
Developers can plan for long-term profitability by designing a flexible layout accommodating various types of businesses or the conversion of a lot to a different use. For instance, some developers have found success in building multi-use facilities that can serve both as an IOS lot and a future warehouse. This approach maximizes the potential of the property and allows for future expansion without the need for additional land purchases. Another owner may convert a lot into a convenience store later, since its location would accommodate this use. Additionally, incorporating sustainable features can increase the lots appeal to potential tenants.
7. Consider Surfacing Options
Traditional surfacing methods such as concrete or asphalt can be costly, but alternative options are both environmentally friendly and cost-effective. One option is Graded Aggregate Base, a layer of compacted gravel made from recycled materials. Recycled concrete is an additional cost-effective option which can be used as a base layer or as a surfacing material. Recycled Asphalt Pavement is another alternative made from old asphalt pavement that has been milled and crushed.
While these alternative surfacing options can help reduce costs, they may not be suitable for all situations and will carry future maintenance costs. Factors such as AHJ requirements, traffic volume, and the type of trucks using the lot will help determine a surfacing material.
8. Consult a Contractor
One of the key factors in successfully constructing a facility is getting a contractor involved early in the process so they can provide insights into the cost of construction and help you determine whether your rent targets are realistic. By getting market pricing from a contractor, you can plan for realistic financial goals.
Future Trends in Industrial Outdoor Storage Facilities
As the industry evolves, IOS development and permitting will become more integrated into local zoning ordinances. This could impact the permitting process and increase development costs as zoning regulations become more complex and require developers to navigate new rules and requirements. Additionally, the trend toward near shoring and onshoring could have a significant impact on the development of IOS lots. There may be a greater need for transportation and logistics infrastructure, including new drop lots and upgrades of existing facilities.
Successfully Navigating Industrial Outdoor Storage Development Challenges
Industrial outdoor storage is a rapidly growing market, attracting investors and entrepreneurs who see the potential for significant returns on investment while supplying a much-needed product. An experienced engineering consultant can navigate the complexities of the permitting process and ensure that the facility meets the current and future goals. This will not only help avoid costly mistakes but also ensure the facility’s long-term success.
Contact us today to learn more about how we can help you build successful industrial outdoor storage facilities that maximize your return on investment.
About the Authors
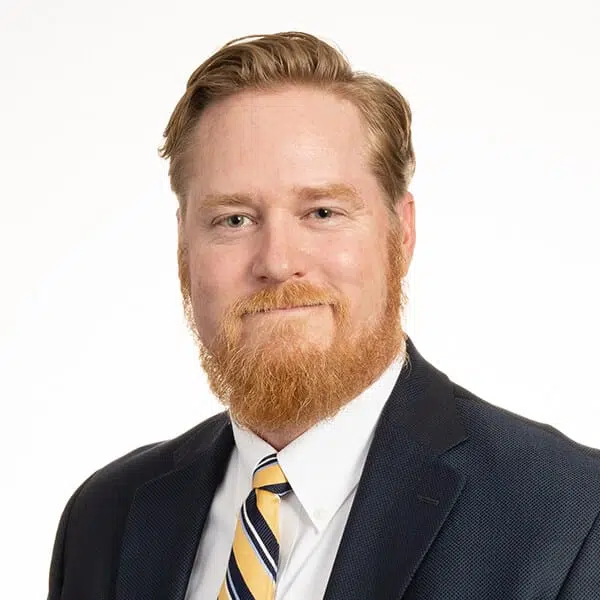
Dave France, PE
Dave is a civil engineer with more than 30 years of experience in commercial and industrial development, with his industrial projects including high-profile developments for clients such as the U.S. Navy Exchange, Ace Hardware, BMW, and large e-commerce and traditional retailers. His work spans master planning, schematic design, site selection, feasibility studies, and roadway design, and he has partnered with local economic development agencies, brokers, developers, and owners on his projects.

Austin Watts, PE
Austin is a senior civil engineer and project manager with more than 20 years of experience managing multidisciplinary teams on commercial and industrial projects across the US. He has provided services on big box commercial and industrial projects throughout the Southeast, Midwest, and West, specializing in entitlement/special use public hearings, erosion and sediment control systems, and utility design.