- January 14, 2021
- Perspectives
Full-Depth Reclamation: Sustainable Asset Management Reduces Costs and Saves Time
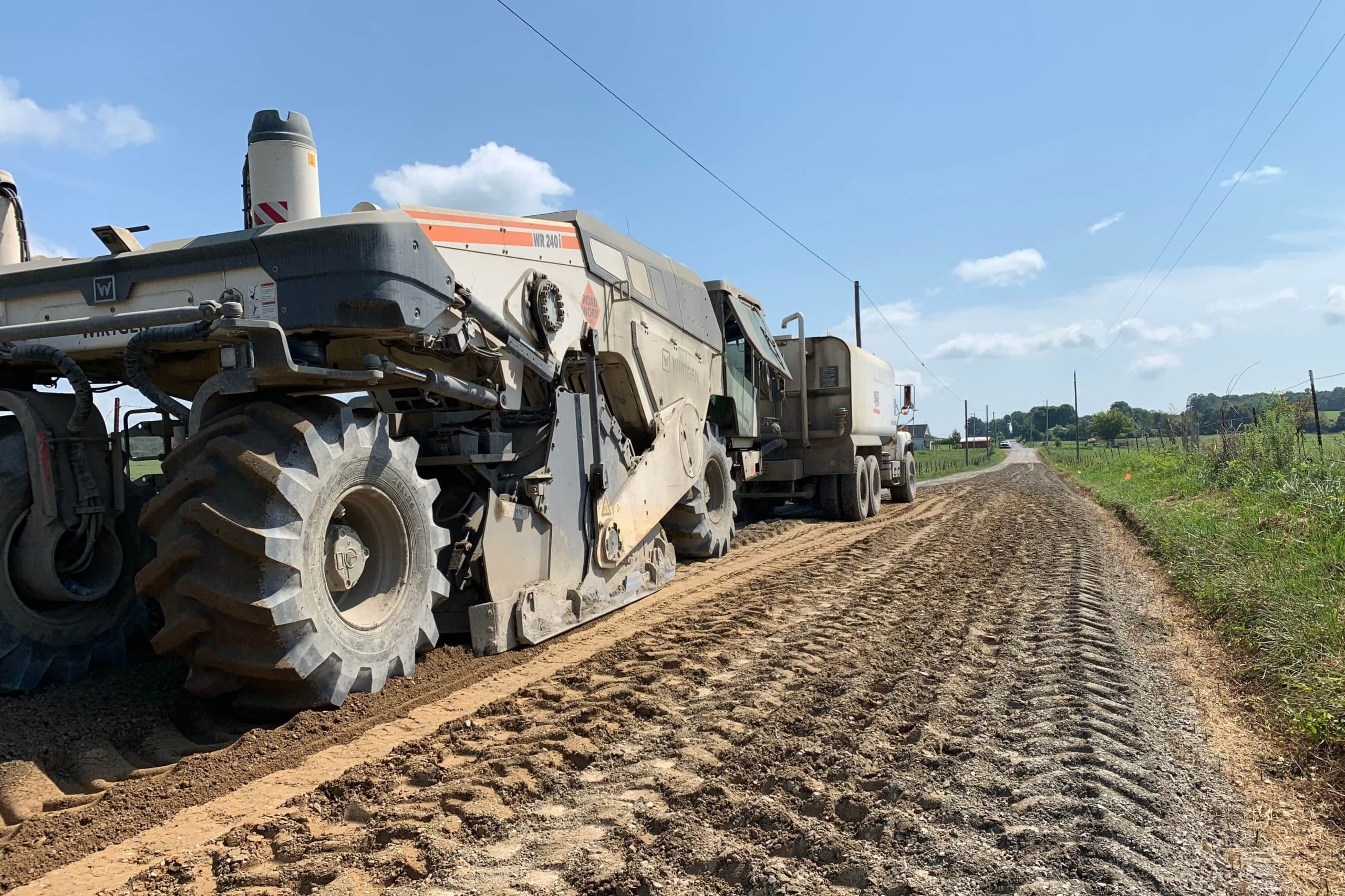
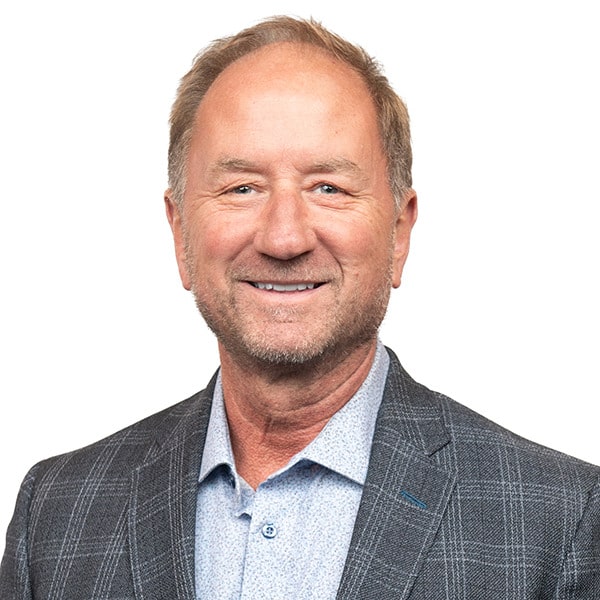
Scott Sounart, PE
Senior Project Manager
Nearly 400 million tons of asphalt pavement are replaced in the United States every year, which amounts to enough asphalt to pave a four-inch thick, two-lane highway around the world six times! The average life span of an asphalt roadway is 15 years. So, what happens to the 6 billion tons of asphalt replaced in those 15 years?
Read on to discover the benefits of recovering renewable materials to minimize environmental impacts, lessen traffic disruptions, and reduce overall asset management costs.
What is Full-Depth Reclamation
In conventional pavement replacement and mill and overlay methods, old asphalt is milled, reprocessed, and reused as recycled asphalt pavement (RAP) for new roads while unused asphalt is stockpiled and repurposed or landfilled. Full-Depth Reclamation (FDR), on the other hand, is the process of pulverizing all layers of existing asphalt pavements in place to depths of up to 20 inches. FDR has grown in popularity as equipment has evolved and recycling efforts have heightened.
Historically, asphalt pavement thickness was designed and constructed based on traffic volume and the strength of the underlying subgrade, often resulting in asphalt thicknesses of 6 to 12 inches. In the 1970s, construction techniques evolved and asphalt pavements were designed as composite sections, which included an aggregate base layer sandwiched between a thinner, less costly asphalt layer and the underlying subgrade.
Aggregate base materials are becoming scarcer and more expensive, but with new technologies, roadway owners and paving contractors are not limited to exclusively using these costly materials in our pavements. Over the last decade, the paving industry has evolved to utilize an abundance of materials for new pavements, many of which involve repurposing existing asphalt.
With FDR, pulverized layers are reclaimed to provide a homogeneous base layer to support a new, thinner surface layer section of asphalt. FDR is best for high severity distressed or failed pavements, where rehabilitation methods are not enough to rejuvenate the pavement. For added stability, the reclaimed base layer can be chemically or mechanically stabilized. Chemical stabilization introduces cement, lime, kiln dust, or emulsified asphalt to improve binding of the materials. Mechanical stabilization adds other aggregates or RAP to strengthen the reclaimed base.
What is Full-Depth Reclamation
Roadway owners and paving contractors are realizing the benefits of FDR as this eco-friendly technology grows in practice:
- Cost Savings: As more robust and improved reclaimers and pulverizing equipment become available, prices will likely decrease, making FDR more viable than traditional reconstruction practices. Additional cost savings are realized through less equipment and materials used, fewer construction personnel, and more pavement service life.
- Time Savings: Construction time is shorter with less disruption to the end user. FDR’s single process of reclaiming existing materials in place typically takes one-third of the time of traditional methods, which require multiple processes such as removal, hauling, re-preparing the subgrade, and replacing with new aggregate base.
- Reduced Impact: FDR has fewer construction obstacles than traditional pavement rehabilitation methods. With less equipment and fewer haul trucks confined to a reduced construction footprint, traffic impacts are lessened during construction on a roadway and downtime for parking lots is minimized.
- Stronger Structures: FDR increases flexibility and strength, while decreasing susceptibility to moisture and rutting potential. Deeper subgrade and base failures can be repaired through FDR.
- Reduced Waste: Since all the site’s material is recycled, unnecessary waste is prevented, resulting in less waste in our landfills. Fewer trucks lead to a reduction in fuel consumption and emissions.
FDR Considerations
While implementing the FDR process, these practices should be considered:
Recovering renewable materials in a perpetual manner is becoming common practice, with benefits including reduced environmental impact, lessened traffic disruption during construction, and overall cost reduction. Our experts have decades of experience in pavement rehabilitation and management and are constantly seeking new and improved methods of managing pavement. To learn more about eco-friendly pavement rehabilitation options, contact Scott Sounart.
About the Expert
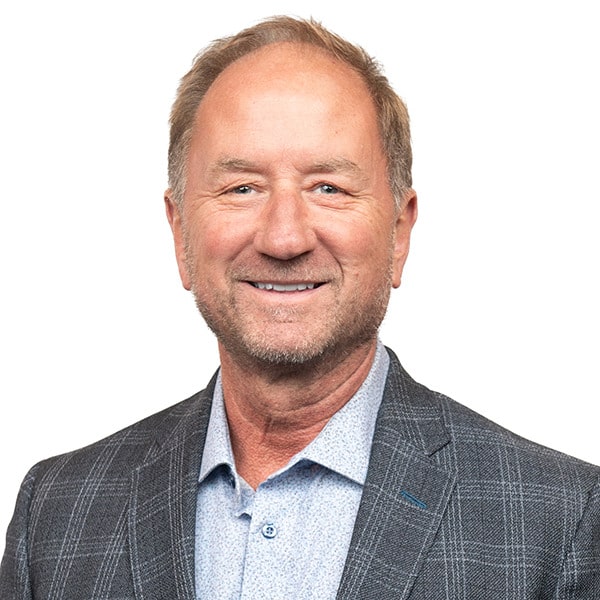
Scott Sounart, PE
Scott has more than 30 years of experience in the design, management, and construction of civil projects ranging from roadways to bridges to airports. He specializes in pavement engineering technologies and has coordinated several research projects related to aggregates and asphalt paving materials, conducted forensic evaluations, and provided expert witness services. His experience includes pavement evaluation studies and designs, pavement and asset management implementations, and distress data collection methods for local and state agency, aviation, and rail clients.